Wstęp
Aby zrozumieć możliwości systemu zacząć trzeba od poznania realizowanych przez niego funkcji. Niektóre są podstawą jego pracy, inne są opcjonalne. Różne maszyny mogą korzystać z różnych zestawów funkcjonalności o różnych konfiguracjach.
Podstawowe funkcjonalności:
- System liczący cykle przeliczane na produkt i czas efektywnej ( rzeczywistej ) pracy
- System statusu określającego jaki stan ma TERAZ maszyna, czy jest w stanie postoju, awarii, przezbrajania czy pracy.
Kiedy aktualnym stanem jest PRACA to czas trwania tego stanu dzielony jest przez system liczący na efektywną pracę, mikropostoje i czas nieoznaczony który mówi: maszyna nie pracuje ale nie wiem dla czego bo nie zmieniono statusu
- System zleceń produkcyjnych które pozwalają nie tylko śledzić ich realizację ale nadają kontekst pracy maszyny. Dzięki zleceniu system między innymi wie jaki jest aktualny, optymalny czas 1 cyklu
niektóre inne funkcje:
- Powiadomienia i komentarze – pozwalają na śledzenie ( chronologiczne ) wszystkich zmian w systemie wraz z komentarzami obsługi
- Operatorzy przypisani do maszyny
- Kalkulacja wskaźników KPI
- Rejestracja / liczenie braków wraz z ich klasyfikacją
- System wezwań pomocy Andon
i inne …
Operator i użytkownik
Użytkownik systemu, konta, uprawnienia
Należy rozróżnić pojęcie operator i użytkownik.
Użytkownik to każda osoba która ma uprawnienie do dokonania jakiejkolwiek czynności w systemie.
Operator zaś to ten użytkownik który w danej chwili jest przypisany do danej maszyny / maszyn.
Wszystkie zapisywane informacje oznaczane są nazwiskiem operatora który przypisany jest do maszyny.
Dzięki czemu możliwe jest tworzenie raportów w kontekście poszczególnych operatorów.
Wszystkie powiadomienia sygnowane są i nazwiskiem użytkownika który w danej chwili jest operatorem maszyny
jak i nazwiskiem użytkownika który operację wykonał (mogę zmienić status maszyny choć nie jestem jej operatorem).
Operator maszyny
Każdej z maszyn można przypisać operatora. Jeden operator może być przypisany do wielu maszyn jednak
do jednej maszyny może być przypisany tylko jeden.
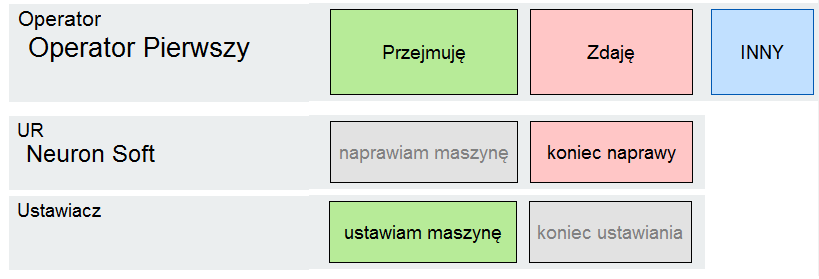
Odbywa się to w ten sposób że operator ( przyciski na panelu operatora) przejmuje albo zdaje maszynę.
Przejmuje, czyli powiadamia system ze on od TERAZ jest operatorem tej maszyny.
Kiedy do pracy przychodzi następny pracownik to on przejmuje maszynę i to on od tego momentu będzie jej operatorem.
Operator zdaje maszynę wtedy gdy po nim nie będzie innego operatora, na przykład zakład kończy pracę.
Pracownik UR
Pracownik UR ( utrzymania ruchu ) to pracownik który w danej chwili naprawia daną maszynę.
Tak jak operator przypisany jest do maszyny tak pracownik UR przypisany jest do niej na czas naprawy.
Ustawiacz
Ustawiacz to pracownik który w danej chwili przezbraja daną maszynę.
Tak jak operator przypisany jest do maszyny tak „Ustawiacz” przypisany jest do niej na czas jej przezbrajania czyli np. zmiany osprzętu wymienianego podczas zmiany zlecenia.
Nazwę „Ustawiacz” można zmienić.
Zarówno pracownik UR jak i Ustawiacz są funkcjami opcjonalnymi.
Status
Status i status rozszerzony
Status - metody sterowania
Co jest głównym celem systemu Golem OEE MES? Dostarczenie informacji o pracy maszyn ? Nie. Głównym celem systemu jest dostarczenie informacji o tym DLACZEGO dana maszyna nie pracuje.
Głównym narzędziem dla uzyskania tego celu jest status - czyli informacja od obsługi o stanie w którym w danej chwili znajduje się dana maszyna. Dlaczego w danym momencie nie pracuje a jeśli pracuje to z jaką efektywnością.
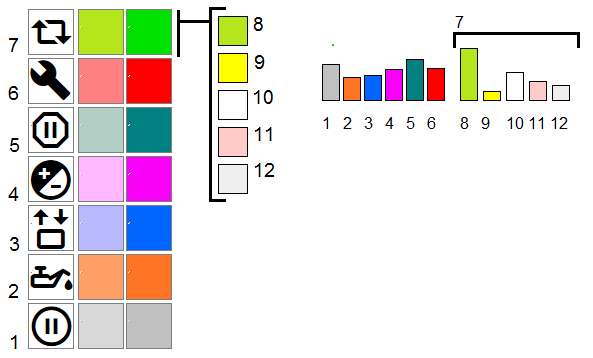
Cały czas życia maszyny dzielony jest na 7 części zwanych statusami.
- Postój planowany – maszyna nie pracuje bo nie ma dla niej żadnych zadań
- Konserwacja – maszyna ma przerwę na planowane lub konieczne czynności konserwacyjne
- Przezbrajanie – zmiana osprzętu lub konfiguracji, np. podczas zmiany produktu
- Ustawianie - podobnie jak przezbrajanie ale dla czynności wymagających mniejszego nakładu pracy
- Postój nieplanowany – postój którego nie planowanego ale nie jest postojem technicznym
- Awaria – maszyna nie pracuje z powodów technicznych
- Praca – a w zasadzie gotowość do pracy
Czas statusu PRACA dzielony jest automatycznie na następujące części:
- Efektywna praca
- Mikro postoje
- Czas nieoznaczony
- Przerwa technologiczna Pt1 – stan wyzwalany wejściem
- Przerwa technologiczna Pt2 – stan wyzwalany wejściem
Doprecyzowania wymaga status PRACA
Kiedy maszyna jest w statusie PRACA (wybrano taki status) to oznacza że POWINNA PRACOWAĆ. Nie oznacza to jednak że pracuje.
Czas pracy dzielony jest przez system automatycznie na:
- Efektywną pracę – maszyna rzeczywiście pracuje
- Mikro postoje – czas składający się z krótkich przerw w pracy
- Czas nieoznaczony – maszyna nie pracuje ale system nie wie dlaczego bo nie zmieniono statusu na inny
- Czas przerw technologicznych sterowanych wejściami – opis niżej
Wykres statusu
Status rozszerzony
Dla poszczególnych maszyn lub grup maszyn ( konkretnie dla określonego modelu ) możemy zdefiniować status rozszerzony. Status rozszerzony składa się z dwu części: statusu głównego i rozszerzenia statusu.
Definiujemy np. status rozszerzony awaria : awaria robota.
Jeśli wybierzemy ten status to jednocześnie zmienimy status podstawowy na awarię i status rozszerzony na awarię robota.
Przykład wykresu pareto statusu rozszerzonego dla wybranego okresu:
Sposoby sterowania statusem
Status zawsze zmieniany jest w czasie rzeczywistym. Nie można ustawić że awaria było do 11:20.
Awaria jest od momentu gdy zmieniono status na awarię i trwa (naliczany jest czas awarii) do momentu gdy zmienimy status na inny.
Podstawową metodą zmiany statusu jest zmiana z panelu operatorskiego programu głównego.
Wygląd panelu zależy od tego czy stosujemy status podstawowy:
czy jest to status rozszerzony:
Po wybraniu nowego statusu program prosi o zatwierdzenie i ewentualny komentarz:
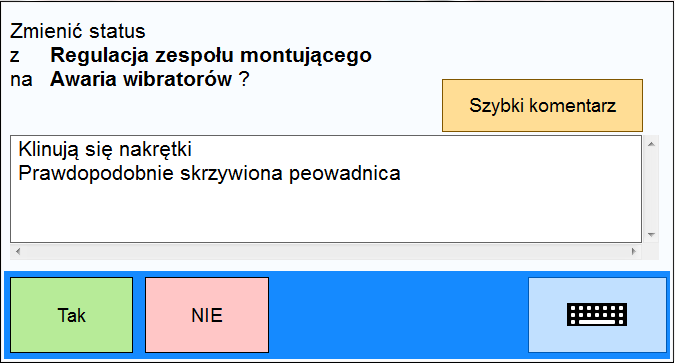
Dostępne są też inne metody zmiany statusu:
- Status nie jest zmieniany – zawsze praca
- Status zmieniany z aplikacji mobilnych – w prawie identyczny sposób jak w programie klienckim
- Status starowany wejściami – status jest kodowany „dwojkowo” za pomocą 2,3, lub 4 wejść
- status sterowany za pomocą rozkazów w skrypcie sterującym stacji
Przerwa technologiczna
Status - przerwa technologiczna
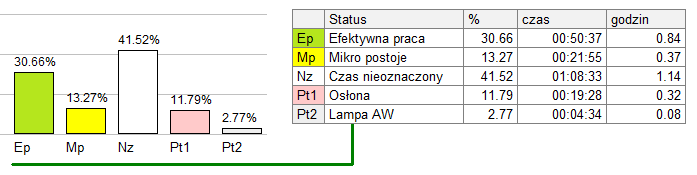
Kiedy aktualnym statusem jest status PRACA to system dzieli ten czas na efektywną pracę, mikro postoje, czas nieoznaczony oraz, opcjonalnie na dwa czasy dodatkowe zwane przerwą technologiczną które sterowane są oddzielnymi wejściami.
Przykładowo możemy zdefiniować przerwę technologiczną „otwarta osłona”, podłączyć do wejścia sygnał otwarcia osłony
i gdy ten sygnał się pojawi, ale tylko podczas statusu PRACA to będzie naliczany czas pt1
Efektywny czas pracy maszyn, mikro postoje
Kiedy maszyna jest w statusie PRACA (wybrano taki status) to oznacza że POWINNA PRACOWAĆ. Nie oznacza to jednak że pracuje. Dlatego system dzieli automatycznie czas przeznaczony na pracę na czas efektywnej pracy, mikro postoje i czas nieoznaczony.
Czas mikro postojów to czas który „się uzbierał” z krótkich przerw. Mikro postoje są liczone po zakończeniu liczenia czasu efektywnej pracy przez czas ustalony w konfiguracji lub krotność czasu cyklu.
Czas mikro postojów może być dobrany tak aby wskazywał nam spadek wydajności ( cykl dłuższy od zakładanego ) albo tak aby wskazywał na operacje robione co jakiś czas. Przykładowo prasa wykrawa co kilka sekund elementy ale co kilka minut należy zmienić pojemnik co może trwać 2 minuty. Jeśli system policzy nam w ciągu zmiany 40 minut mikro postojów to możemy domniemywać że czas ten wykorzystany był na tego typu czynności.
Czas nieoznaczony to czas w którym maszyna nie pracuje ale system nie wie dlaczego bo nikt nie zmienił statusu.
Metody pomiaru czasu efektywnej pracy
Dostępne są dwie metody liczenia (pomiaru) efektywnego czasu pracy.
Pierwsza metoda polega na tym że czas pracy „biegnie” gdy załączone jest wejście koncentratora:

Poprzez analogię to tak jakbyśmy podłączyli klasyczny licznik czasu pracy.
Jednak w większości maszyn nie ma sygnału który byłby adekwatny do faktycznego czasu pracy.
Powiedzmy ze maszyna to prasa a sygnał to impuls z zaworu załączającego sprzęgło. Gdy sprzęgło zadziała praca wykonuje cykl.
Cykl taki zależnie od wielkości pracy i jej narzędzi może trwać powiedzmy 4 sekundy.
No ale impuls załączający zawór który doprowadzamy do koncentratora trwa np. 0.5 sekundy.
Dlatego druga metoda liczenia czasu pracy polega na doliczaniu ustalonego czasu po impulsie (wykryciu zbocza narastającego sygnału):
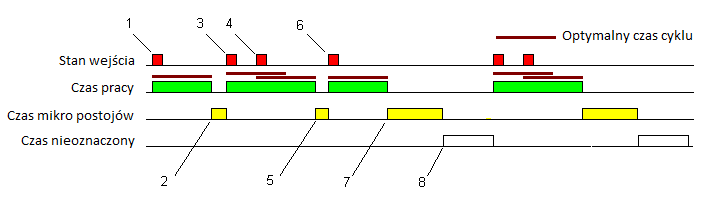
Czas ustalony jest na stałe (czas Tt z modelu ) albo jest parametrem zlecenia – tzw. optymalny czas cyklu.
Kiedy podamy napięcie na wejście (1) program zaczyna liczyć czas pracy przez czas OCC. Kiedy czas ten się skończy a w międzyczasie nie pojawi się następny impuls to zaczyna być liczony czas mikro przestojów (2).
Następny impuls (3) przerywa czas mikro przestojów i ponownie naliczany jest czas pracy.
Ponieważ następny impuls (4) pojawił się zanim miną czas OCC to czas pracy liczony jest od nowa.
Kolejny impuls (6) pojawił się już po czasie OCC więc naliczony został czas mikro przestojów (5).
Po upływie czasu OCC naliczany jest ponownie czas MP (7).
Kiedy skończy się liczenie czasu MP a nadal nie ma sygnału na wejściu to liczony jest czas nieoznaczony (8)
Operacja, cykl, produkt
Operacja, produkt, cykl, wydajność
Jedną z funkcji systemu jest liczenie ilości wyprodukowanej. A tak naprawdę liczenie ilości wyprodukowanej w kontekście czasu – ile wyprodukowano tego samego produktu wczoraj a ile dzisiaj, ile w ramach dwu podobnych zleceń itp.
Najpierw rejestrujemy cykle maszynowych, np. prasa wykonała „uderzenie”. Każdy cykl powoduje zwiększenie licznika produkcji o aktualną krotność, np. wykrojnik wycina 6 elementów więc każdy cykl maszynowy powoduje zwiększenie ilości produktu o 6 szt.
Możemy też zastosować operacje które powodują że potrzeba kilku impulsów wejściowych na jeden cykl. Np. maszyna 16 razy zgrzewa materiał aby wykonać jeden segment.
Wydajność
Aktualną wydajność liczymy w ten sposób że przez ustawiony czas system zlicza wykonany produkt a potem wylicza ile powinno być na godzinę przy takim tempie produkcji.
Na podstawie bieżącej wydajności kreślony jest 72 godzinny trend wydajności z krokiem 4 minut.
Czas cyklu, czas od początku cyklu, czas pakietu

Czas cyklu wyliczany jest jako średnia ważona z ostatnich trzech cykli. Aktualny czas cyklu wraz z czasem podstawy prezentowany jest na wykresie wraz z współczynnikiem CTR który CTR określa o ile procent cykl jest dłuższy lub krótszy od cyklu założonego.
Mierzony i pokazywany jest też czas od początku cyklu. Możemy odczytać czy ostatni cykl rozpoczął się kilkanaście sekund temu czy może kilka godzin temu.
Mierzony jest też czas od początku pakietu cykli który mówi nam ile czasu maszyna pracuje bez przerwy dłuższej niż czas mikro postoju
Arytmetyczna wydajność i czas cyklu
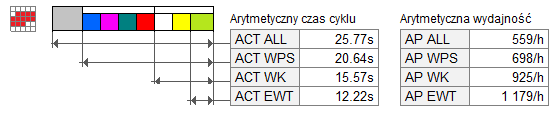
Czym różni się produktywność od wydajności? Nie da się pracować cały czas z maksymalną wydajnością.
Arytmetyczny czas cyklu i arytmetyczna wydajność obliczane są w kontekście czasu efektywnej pracy [EWT], czasu przeznaczonego na pracę [WK], czasu bez postojów planowanych [WPS] i całego czasu [ALL] dla którego prowadzone są obliczenia.
inaczej mówiąc możemy zobaczyć jak straty i postoje planowane wpływają na rzeczywistą wydajność i czas cyklu.
Inspektor cyklu
Inspektor cyklu
Inspekcja cyklu to specjalne, dodatkowe narzędzie które pozwala na wyrywkowe śledzenie każdego cyklu maszyny.
Zaznaczmy wyraźnie że mowa o długich cyklach, przekraczających kilka a czasem sięgających i kilkadziesiąt minut
choć jest możliwa praca w trybie rejestrowania pakietów cykli dla maszyn z krótkim cyklem.
Rejestracja cyklu dla inspektora odbywa się na życzenie – trzeba ją dla każdej maszyny ręcznie załączyć.
Przykładem zastosowania może być śledzenie pracy maszyn CNC gdzie typowy cykl trwa kilka - kilkanaście minut.
Gdy mamy podejrzenia że praca nie odbywa się zgodnie z technologią załączyć możemy inspekcję cyklu i rejestrować
każdy z nich wraz z czasem trwania i informacją o czasie poprzedzającym cykl.
wykres opisującyjeden cykl
Powiadomienia
Podział powiadomień, zdarzenia

Widoczne powiadomienia możemy podzielić ( filtrować ) na:
- widoczne są wszystkie powiadomienia
- powiadomienia związane z produkcją: zmiany statusu, komentarze związane z produkcją, zmiany operatora i ustawiacza, zmiany zlecenia.
- powiadomienia związane z utrzymaniem ruchu: zmiana statusu na awarię i na pracę po awarii, zmiany pracownika UR, wezwania pomocy technicznej
- powiadomienia związane ze zleceniem: zmiany zlecenia, zmiany parametrów, mikroraporty zlecenia
- powiadomienia związane z jakością: dodawanie braków, komentarze oznaczone jako jakość
- powiadomienia związane z logistyką: przywołanie pomocy logistycznej, korekty stanu marketu
- powiadomienia inne: komentarze inne.
- przełącznik EV powoduje widoczność zdarzeń nie będących powiadomieniami
Niektóre zdarzenia nie są powiadomieniami. Są ukryte i aby je zobaczyć trzeba załączyć przełącznik EV Takimi zdarzeniami są: dodawanie braków przez operatora, aktualizacja stanu marketu czy mikroraporty zmianowe.
Komentarze
Komentarze są integralną częścią powiadomień. Każda operacja wykonana przez operatora lub użytkownika skutkuje dodaniem do rejestru powiadomienia a prawie każde powiadomienie może zostać opisane komentarzem.
Przykładowo gdy operator zmienia status to pojawia się okno z pytaniem TAK/NIE i miejscem na wpisanie komentarza.
Można też dodać komentarz który będzie umieszczony w rejestrze jako samodzielne powiadomienie. W takim przypadku określamy też temat, np. jakość, co może być użyte przy filtrowaniu powiadomień.
Szybkie komentarze
Możemy zdefiniować listę tzw. szybkich komentarzy dla opisu częstych zdarzeń. Szybki komentarz działa podobnie jak zwykły komentarz ale nie jest wpisywany ręcznie tylko wybierany z listy.
Podczas edycji listy szybkich komentarzy możemy przypisać do pozycji model nadzorcy – na liście widoczne będą komentarze bez przypisanego modelu oraz te z modelem z którego wywodzi się nadzorca wybranej maszyny – szczegóły w opisie konfiguracji.
Mikro raport w powiadomieniu
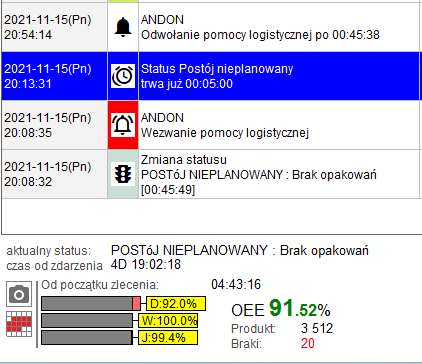
Podczas generowania każdego powiadomienia tworzony jest mikro – raport który do tego zdarzenia jest dołączony.
Jeśli aktywne jest zlecenie to jest to mikro – raport dla zlecenia, w przeciwnym wypadku dla zmiany roboczej podczas której wygenerowano zdarzenie. W ramach mikro – raportu wyliczane jest OEE i jego składniki, ilość produktu i ilość braków.
Jeśli zdarzenie wygenerowano podczas trwania zlecenia to widzimy również czas od jego rozpoczęcia.
System mailowy
Powiadomienia - wysyłka e-mail
Powiadomienia mogą być wysyłane do wskazanych grup użytkowników jako listy e-mail w ramach tzw. akcji
definiowanych w ustawieniach konkretnej maszyny.
Akcją może być wysłanie informacji o wszystkich powiadomieniach albo tylko o powiadomieniach związanych z utrzymaniem ruchu. Akcją może też być wysłanie maila z raportem końcowym zmiany lub raportem końca zlecenia.
Zdarzenia ON OFF
System może rejestrować zdarzenia załączenia (On) i/lub wyłączenia (Off) wejścia.
Rejestrację zdarzeń stosujemy wszędzie tam gdzie chcemy zapisać że o określonej godzinie zmienił się stan jakiegoś urządzenia.
Mamy na przykład komorę suszarniczą - cykl suszenia trwa kilka godzin – wiedza że w nocy wykonano 3 cykle
niewiele nam mówi – woleli byśmy wiedzieć że cykl wystartował o 2:33 a skończył się o 4:20. A następny o 4:47
Innym przykładem może być rejestracja otwierania osłony w maszynie CNC.
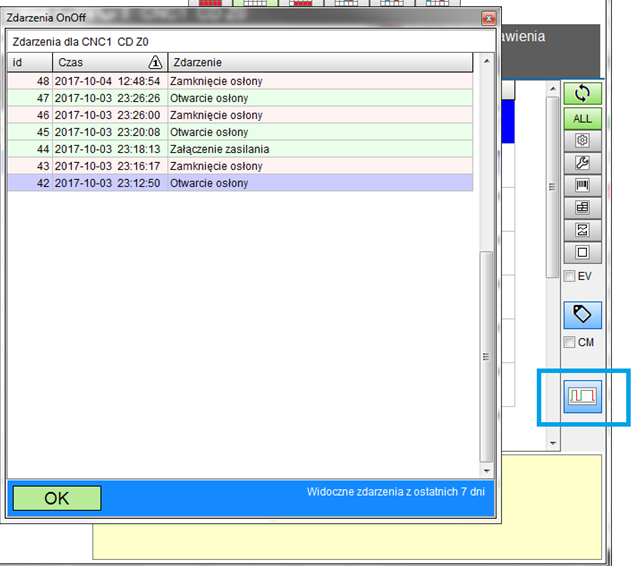
Okno rejestru zdarzeń otwieramy przyciskiem dostępnym w pasku
narzędzi rejestru powiadomień
Braki
Braki, odpad, kalsyfikacja braków
Jedną z funkcjonalności systemu jest liczenie braków, czyli wadliwych produktów. Wiedza o ilości braków obok ilości wyprodukowanej oraz wszystkich czasach (pracy, postoju awarii etc) jest o tyle ważna że decyduje o właściwej ocenie wydajności i efektywności produkcji gdyż braki które powstaną trzeba najczęściej odtworzyć a to kosztuje czas.
Braki do systemu można za pomocą panelu operatorskiego podając ich ilość lub za pomocą asystenta który liczy je, np. korzystając z sygnału wyrzutnika braków systemu wizyjnego.
Możliwy jest podział braków wedle przyczyn ich powstawania.
Korekta braków
Informacja o ilości braków to jedyna informacja w całym systemie która może być korygowana i/lub wprowadzana w innym terminie.
Specjalny formularz

pozwala na odszukanie w bazie danych zapisów z ostatnich 2, 8 lub 20 dni i po identyfikacji odpowiedniego rekordu danych na podstawie czasu, operatora lub zlecenia dodać odpowiednią ilość braków do tego konkretnego rekordu a więc w poczet konkretnego dnia/zmiany lub konkretnego zlecenia produkcyjnego
Wskaźnik OEE
Wskaźniki KPI/UR: OEE, MTTR, MTBF, CAVITY
Wskaźnik OEE jest na tyle ważnym wskaźnikiem KPI że od lat ma on swoje miejsce w nazwie systemu.
System wylicza wskaźnik OEE i prezentuje graficznie za pomocą naszego autorskiego, unikalnego wykresu reprezentującego zależności pomiędzy jego składowymi.
wykres w panelu informacyjnym:
wykres na wydruku raportu:
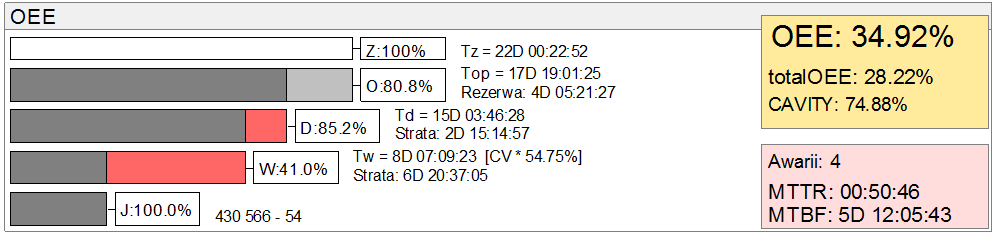
Wskaźnik OEE, szczególnie jego składowe: czas operacyjny, dostępność, wykorzystanie i jakość to bardzo silne narzędzie pozwalające na szybką ocenę pracy maszyn. Nie jest jednak „świętym Graalem” i często wymaga umieszczenia go we właściwym kontekście – szczególnie gdy wyznaczamy go, a Golem to potrafi, dla grupy maszyn, operatorów lub długiego okresu czasu.
MTTR, MTBF, CAVITY
Wraz ze wskaźnikiem OEE wyznaczane są dwa wskaźniki charakterystyczne dla utrzymania ruchu:
MTTR: Średni czas potrzebny do naprawy awarii (ang. Mean time to repair) wyznaczany jako czas awarii / ilość awarii
MTBF: Średni czas pomiędzy awariami (ang. Mean time between failures) wyznaczany jako badany czas / ilość awarii.
Wskaźnik CAVITY ( nazwa od mold cavity – gniazdowość form wtryskowych) wskazuje różnicę pomiędzy ilością wyprodukowaną a ilością która mogła by być wyprodukowana na sprawnym narzędziu.
Powiedzmy że mamy narzędzie o określonej krotności ( ilości produktu na cykl ), niech będzie to forma z 10cioma gniazdami, czyli o krotności 10. Niech ta forma ma uszkodzone jedno gniazdo czyli rzeczywista krotność to 9.
Wskaźnik CAVITY wyniesie 90% czyli wyprodukowano 90% tego co można by wyprodukować gdyby wszystkie gniazda były sprawne.
Na życzenie wskaźnik CAVITY może zostać włączony w skład wskaźnika OEE według formuły:
wykorzystanie = CAVITY (w procentach ) X wykorzystanie.
Czyli jeśli wykorzystanie to 50% a CAVITY = 90% to wykorzystanie wyniesie 90% z 50 czyli 45%
System Andon
Andon to system pozwalający pracownikom na wezwanie pomocy. Wezwanie pomocy widoczne jest na wielu ekranach
programu oraz generuje odpowiednie powiadomienia.
Do dyspozycji mamy pięć rodzajów wezwań:
- wezwanie pomocy
- wezwanie pomocy technicznej
- wezwanie pomocy logistycznej (opcjonalne)
- dwa wezwania o nazwie definiowanej w ustawieniach (opcjonalne)
Wezwanie mogą być generowane z poziomu programu lub za pomocą wejść ( przycisków lub przełączników )
W górnej części okna widoczny jest globalny licznik ilości wezwań pomocy we wszystkich grupach
Wezwania możemy podejrzeć na zakładce Andom:
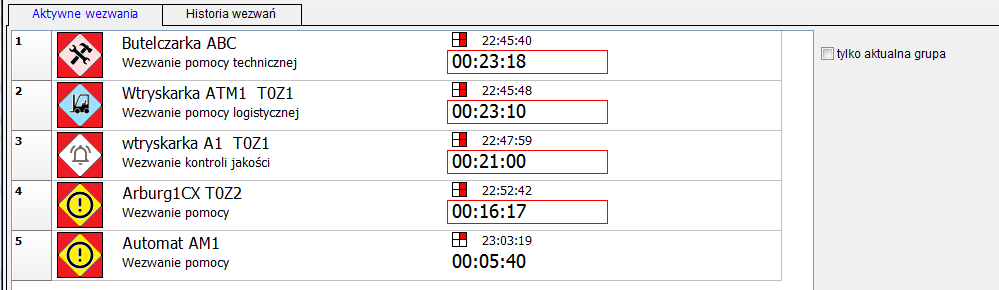
Wezwania są uporządkowane do najstarszych, możemy wybrać czy widoczne maja być wszystkie wezwania czy tylko
wezwania z aktualnie wybranej grupy
Informacje o maszynie
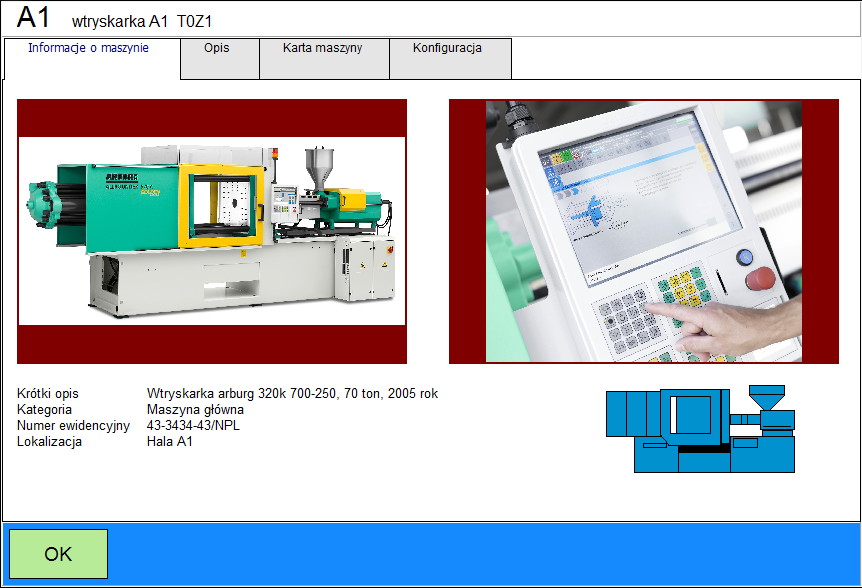
Pierwsze dwie zakładki zawierają opis i zdjęcia maszyny ( edytowane w konstruktorze, w edytorze nadzorcy – przycisk [karta informacyjna] ). Kolejna zakładka zawiera 3 karty maszyny które mogą być edytowane przez operatorów gdzie można tworzyć dowolne notatki. Czwarta zakładka pozwala na podgląd konfiguracji nadzorcy maszyny.
Ab edytować notatki na kartach maszyny musimy użyć przycisku [edytor kart info] w panelu operatora. Karty mają domyślne nazwy karta1, karta2 i karta3 które można zmienić w konfiguracji, np. karta może nazywać się „eksploatacja”.
Pod każdą kartą widoczna jest data ostatniej edycji z informacją kto ją edytował.