Wstęp
Cała idea systemu oparta jest na zasadzie śledzenia pracy maszyny za pomocą jednego sygnału. Gdy jest to maszyna pracująca cyklicznie program śledzi zbocza narastające i po każdym zwiększa odpowiednio liczniki cykli i produktu oraz odlicza ( a w zasadzie dolicza ) czas pracy. Gdy maszyna pracuje w sposób ciągły albo ma długi czas cyklu to czas mierzymy tak długo jak „trwa” sygnał na wejściu.
System ma jednak dużo większe możliwości a wejścia mogą być wykorzystane do realizacji wielu dodatkowych funkcji.
Dlatego przygotowaliśmy ten rozdział jako zbiór różnych porad, uwag i pomysłów czy przykładów rozwiązań różnych problemów związany z podłączeniem maszyn oraz mniej typowych konfiguracji.
Ile sygnałów na maszynę
Koncentratory mają określoną ilość wejść. Naturalnym jest wiec pytanie ile wejść potrzeba na jedną maszynę. Tu są dwie odpowiedzi: prosta i złożona. Prosta – potrzebujemy jedno wejście na jedną maszynę. Złożona – potrzebujemy
co najmniej jedno wejście na maszynę.
Na rysunku widzimy dwie maszyny, jedna wykorzystuje jedno wejścia a druga aż pięć. Monitorujemy pomocniczo pompę hydrauliki i osłonę (momenty jej otwarcia), liczymy też braki sygnałem z systemu wizyjnego i pomiar zużycia energii sygnałem impulsowym licznika energii.
To jednak nie koniec. Możemy wykorzystać dwa, trzy lub cztery wejścia do kodowania statusu maszyny i jedno lub dwa wejścia dla systemu przywoławczego ANDON.
Częstą praktyką jest używanie wielożyłowych przewodów, np. przewodów lan pomiędzy maszyną a skrzynką z koncentratorem co daje nam poza masą 7 żył do wykorzystania nawet gdy w pierwszym projekcie uważamy że starczy nam tylko jeden sygnał.
Ile koncentratorów
System może obsłużyć do 8 koncentratorów wejść. To ile potrzebujemy koncentratorów nie zależy tylko od ilości potrzebnych wejść ale też od przestrzennego rozmieszczenia maszyn. Powiedzmy że mamy 10 maszyn i używamy po jednym sygnale. Wystarczy nam jeden koncentrator 16 wejść.
A teraz wyobraźmy sobie że te maszyny stoją po pięć na dwu halach:
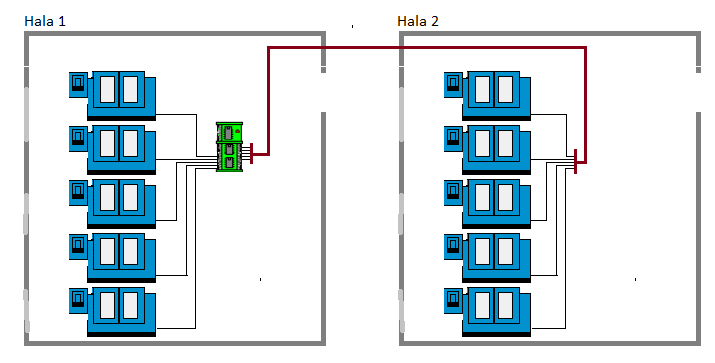
Nadal używamy jeden koncentrator ale musimy „przerzucić” przewód wielożyłowy między halami.
Możemy też zastosować dwa koncentratory które podłączymy np. do sieci LAN via konwertery rs/lan:
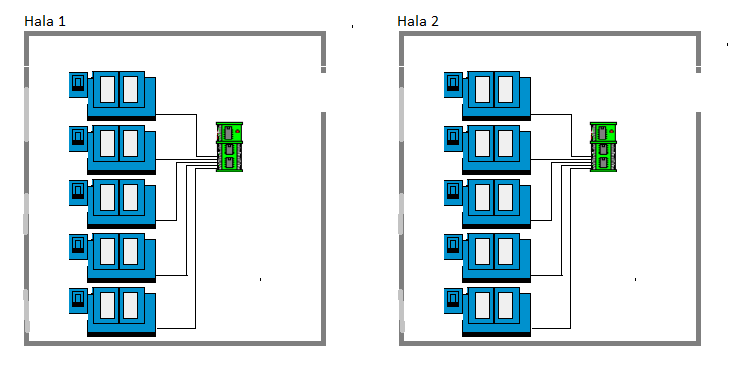
A takich przestrzennych układów może być wiele. Czasem nawet w obrębie jednej dużej hali opłaca się nam zastosować dwa mniejsze koncentratory zamiast jednego dużego.
Jedno wejście, kilku nadzorców
Jednym z parametrów nadzorcy SV jest numer wejścia do którego podłączony jest główny sygnał. Dzięki temu możemy nie tylko swobodnie gospodarować wejściami czy prosto zamienić dwa wejścia jeśli się okaże że się pomyliliśmy ale możemy też ustawić to samo wejście dla kilku nadzorców. Rozwiązanie takie może być szczególnie przydatne na etapie tworzenia systemu testowego – możemy skonfigurować kilka wariantów obsługi tej samej maszyny aby wybrać najkorzystniejszy wariant.
Maszyna vs Agregat
Celem systemu jest monitorowanie maszyn produkcyjnych. Jednak niski koszt dodatkowych wejść powoduje że możemy pozwolić sobie na monitorowanie pracy różnych urządzeń pomocniczych takich jak kompresory, agregaty chłodzące, proste maszyny pomocnicze a nawet oświetlenie hali.
Konfiguracja modelu nadzorcy z wybranym trybem „Agregat” jest dużo prostsza niż trybu „Maszyna”. Sprowadza się do ustawień filtrów, sposobu liczenia czasu pracy, motogodzin, licznika cykli oraz sterowania statusem za pomocą wejść.
Do agregatów możemy przypisać asystentów energii i zdarzeń.
Przykład panelu info dla agregatu chłodzącego:
Linia produkcyjna
Kiedy myślimy o linii produkcyjnej w naturalnym odruchu myślimy o śledzeniu pracy każdej z maszyn w skład tej linii wchodzącej. Jednak przy szeregowej konfiguracji #1:
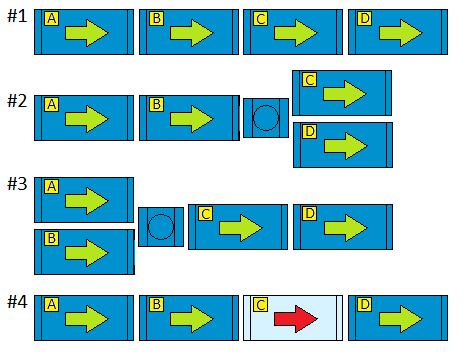
wszystkie segmenty linii wspólnie produkują i jeśli jakakolwiek z maszyn zwolni lub się zatrzyma zwolni lub zatrzyma się cała linia. Nawet jeśli między segmentacji są bufory podtrzymujące jej pracy to rzadko starczą one na kilka sekund.
Dlatego konfiguracja #1 z punktu widzenia systemu to
jedna maszyna a sygnały pobieramy z segmentu D.
Określeniu które segmenty sprawiają większy problem służą odpowiednio zeskalowane statusy rozszerzone.
Z kolei w przypadku konfiguracji #2 z punktu widzenia systemu mamy dwie maszyny, szczególnie gdy segmenty C i D mogą działać niezależnie. Jelśi segmenty C i D zawsze działają „równolegle” to możemy użyć asystentów liczenia o czym niżej.
Konfiguracja #3 z punktu widzenia systemu nie różni się od konfiguracji #1. To segment D „robi robotę” ale dla celów poznawczych możemy rozważyć stworzenie oddzielnych nadzorców dla A i B.
W konfiguracji #4 również pracę wykonuje segment D ale segment C jest uruchamiany warunkowo i możemy śledzić jego pracę aby np. wiedzieć jaki jest stosunek jego czasu pracy do całości linii.
Każda linia produkcyjna jest inna ale zasadą powinno być śledzenie pracy tych jej segmentów które wpływają na końcowy produkt.
Kształtowanie sygnałów filtrami
W konfiguracji każdego modelu / nadzorcy mamy do dyspozycji trzy filtry: filtr opóźnienia załączenia, opóźnienia wyłączenia i filtr blokady. Sposób ich działania opisano w rozdziale „podłączenie maszyn: - tu kilka praktycznych wskazówek ich wykorzystania:
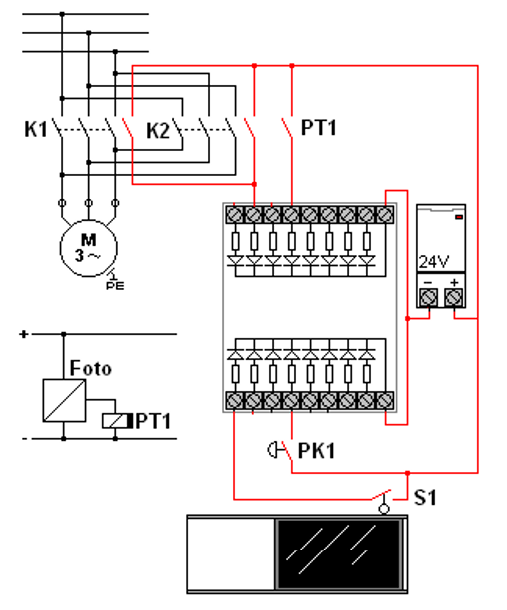
Użycie filtru opóźnienia wyłączenia: mamy maszynę której napęd cyklicznie zmienia kierunek. Sygnał dla systemu pobraliśmy używając styków pomocniczych styczników K1 i K2 – czyli sygnał mamy gdy napęd obraca się w prawo lub w lewo. Występuje jednak problem gdy sygnał zanika na chwilę w momencie zmiany kierunku, kiedy wyłącza się jeden stycznik mija jakiś krótki czas zanim załączy się drugi. Powstaje wtedy przerwa w sygnale którą chcemy wyeliminować. Wystarczy wtedy ustawić 2-4 sekundy w filtrze opóźnionego wyłączenia – wtedy przerwa na zmianę kierunku zostanie przez system zignorowana.
Kolejnym przykładem jest sygnał z przycisku którym operator „kwituje” wykonanie jakiejś czynności. Montuje jakiś agregat a gdy go skończy to naciska przycisk GOTOWE (PK1).
Człowiek który naciska przycisk nie widzi skutków swojego działania więc naciska go kilkukrotnie. A my chcemy jeden wpis do rejestrów a nie kilka. Dlatego użyjemy filtr blokady i ustawimy go np. na 10s. Dzięki temu system po naciśnięciu przycisku będzie przez 10 sekund ignorował przychodzące sygnały.
Trzecim przykładem jest osłona maszyny. Czujnik S1 działa w taki sposób że podaje sygnał do koncentratora kiedy osłona jest otwarta. Ale operator często otwiera osłonę na kilkanaście sekund co jest normalną czynnością eksploatacyjną. My chcemy mieć raport o sytuacji gdzie operator otworzy osłonę i ją tak pozostawi.
Ustawiamy więc filtr opóźnienia załączenia na 30 sekund – system „zobaczy” że osłona jest otwarta jeśli będzie ona otwarta co najmniej 30 sekund.
Kiedy jednak chcemy raportować każde otwarcie osłony to ustawiamy filtr blokady, tak jak w przykładzie z przyciskiem ale na 2-3 sekundy aby wyeliminować ewentualne fałszywe sygnały przy domykaniu osłony.
Kiedy do czynienia mamy bardzo krótkie sygnały ( filtr koncentratora traktuje krótkie sygnały jak zakłócenia i je ignodruje) możemy skorzystać z zewnętrznych przekaźników czasowych.
W powyższym przykładzie taki przekaźnik (PT1) wykorzystano do kształtowania sygnału z przekaźnika fotoelektrycznego do wycinania bardzo krótkich sygnałów rzędu części sekundy z którymi filtry golem a sobie nie poradzą.
Do kształtowania sygnałów możemy też wykorzystać sterowniki PLC o czym niżej.
Sterowanie statusu wejściami
To trochę kontrowersyjny temat bo często sterowanie statusem za pomocą wejść, czytaj przełączników kodujących czy sygnałów z maszyn nie jest optymalną opcją a wynika z niczym nieuzasadnionej niechęci dawania pracownikom „dostępu do komputera” choć są oczywiście uzasadnione przypadki wynikające np. z warunków środowiskowych.
Trochę inaczej jest w przypadku trybu „Agregat”. tam sterowanie statusu wejściami jest wpisane w DNA i nie ma innej opcji.
Status podstawowy
Status podstawowy kodujemy jednym (A), dwoma (AB) lub trzema (ABC) wejściami koncentratora wg następującego kodu:
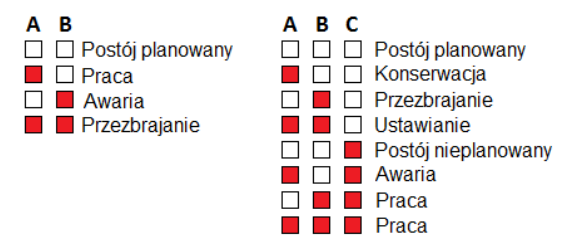
i przykład użycia ogólnodostępnych przełączników do jego kodowania
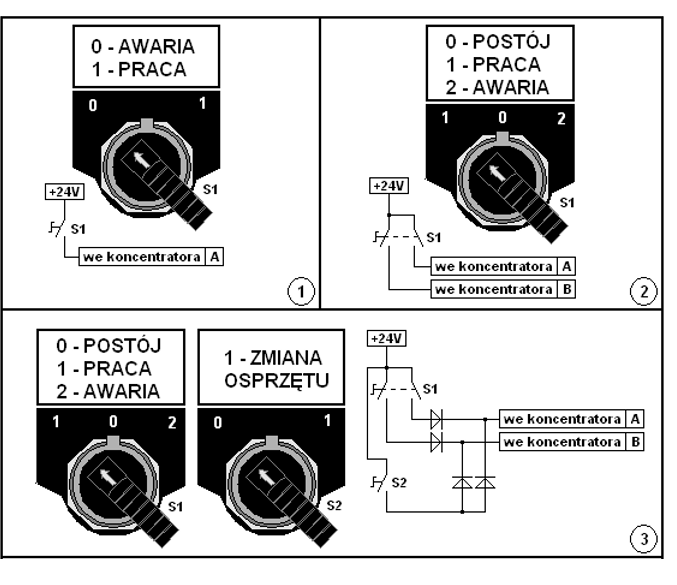
Wyjaśnienia wymaga kodowanie jednym wejściem które zarezerwowane jest dla trybu Agregat i zależnie od konfiguracji koduje stan postój / praca i awaria / praca. W praktyce stosować go będziemy nie z użyciem przełącznika a sygnałów.
Np. brak sygnału może oznaczać PRACĘ a sygnał pobrany z zabezpieczeń, np. z zabezpieczenia silnika wymusi stan AWARIA.
W ten sposób przechodzimy do sterowania statusem za pomocą sygnałów z maszyny:

Sygnał przełączający między wejściami A i B pochodzi z przekaźnika podłączonego do lampy sygnalizującej awarie, ale poprzez przekaźnik podłączony do zasilania maszyny – nie ma zasilania – mamy status Postój planowany, jest zasilanie ale nie ma sygnału awarii mamy status Praca. Dodatkowo możemy podłączyć przełącznik przezbrajanie jeśli jest wskazany dla danego urządzenia.
Trzeba jednak zachować
dużą rezerwę dla tego typu rozwiązań. Gdy o statusie „awaria” melduje operator to zapewne jest on o awarii przekonany. Zmieniając status mówi
Sprawdziłem co sprawdzić mogłem, od tej chwili odpowiedzialność za maszynę przechodzi w ręce służb UR
Co mówi nam status awaria wyzwolony lampą? Tyle że maszyna się zatrzymała. Nie wiemy czy się coś zacięło, zepsuło czy zabrakło materiału. No i to zdziwienie że na jednej zmianie awarii było czterdzieści.
Status rozszerzony
Status rozszerzony możemy sterować 3 (A,B,C) lub 4 (A,B,C,D) wejściami. Nie ma na stałe określonej kombinacji wejść – definiując w modelu poszczególne pozycje dla każdej definiujemy kombinację wejść:
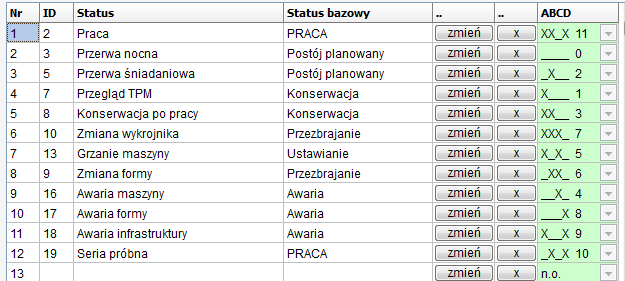
Jak widać poszczególne wartości ( X to logiczna jedynka, _ to logiczne zero, obok kod BCD ) nie muszą być przypisane w określonym porządku.
Niestety nie jest łatwo pozyskać wielopozycyjne, aparatowe przełączniki BCD. Można zastosować nastawniki kodujące BCD, takie jak w starych regulatorach ale są one dość delikatne. Są różnego rodzaju przełączniki wielopozycyjne często z różnym kodowaniem ( stąd możliwość ustalania kolejności ) ale rzadko mają one więcej niż 7 pozycji.
Niemniej kodowanie ABCD może być wykorzystane do sterowania np. za pomocą wyjść sterownika PLC ( patrz niżej ).
Nas partnerzy mają też swoje indywidualne rozwiązania, klawiatury mikroprocesorowe które wystawiają odpowiednią kombinację na wyjściach:
Asystent statusu, skrypty
Pamiętajmy że sterując statusem za pomocą wejść to rozwiązanie albo / albo. Sterowanie wejściami ABCD odbiera nam możliwość sterowania statusem za pomocą programu czy aplikacji i ma kilka istotnych wad: nie wiemy kto zmienił status i nie wiemy dlaczego – brak komentarza.
Istnieją jednak metody aby zmienić status obsługiwany z programu czy aplikacji za pomocą wejść. Pierwsza to sterowanie z wnętrza skryptu sterującego stacji. Ma on komendy które „udają” operatora. Możemy obserwować stan wejścia i nadzorcy i po spełnieniu odpowiednich warunków wysłać do systemu polecenie zmiany statusu. Wymaga to jednak podstawowych umiejętności programowania i zrozumienia czym jest programowanie asynchroniczne.
Można też skorzystać z asystenta statusu. Działa on tak że wykrywając zbocze narastające sygnału na wejściu wymuszone zostanie ustawienie wybranego statusu. Można też określić że asystent ma zadziałać tylko przy określonym statusie.
Wyobraźmy sobie dwa przyciski przy osłonie piły. Jeden przycisk spowoduje wybranie statusu „postój nieplanowany – zapchana piła” ale tylko jeśli aktualnym statusem jest status praca a drugi wybierze status PRACA ale tylko jeśli aktualnym statusem jest „postój nieplanowany – zapchana piła”. Jednak aby takie rozwiązanie było skuteczne operator powinien z tego miejsca widzieć wizualizację stanu maszyny, np. na monitorze nad nią.
Przerwa technologiczna
Kiedy obowiązującym jest status PRACA to system automatycznie dzieli czas tego statusu na efektywną pracę, mikro postoje, czas nieoznaczony oraz czas dwu przerw technologicznych. Przerwy technologiczne sterowane ( aktywowane ) są wejściami, ale tylko podczas statusu praca.
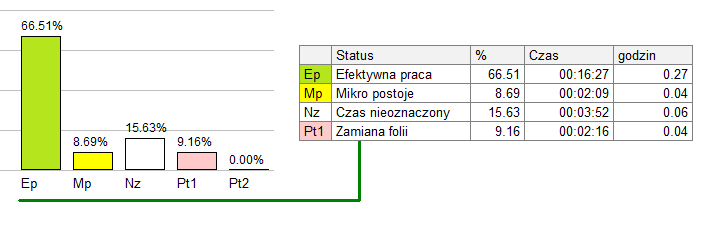
Wyobraźmy sobie pakowarkę która ma system automatycznej zmiany folii. Co kilkaset pakietów pakowarka wstrzymuje pracę aby odpowiedni mechanizm zmienił rolki folii na nowe. O ile są rolki w zasobniku. Jeśli możemy pozyskać sygnał mówiący „trwa zmiana folii” to możemy zdefiniować przerwę technologiczną „Zmiana folii” i śledzić jaki jest udział tego procesu w ogólnym czasie pracy.
Możemy też dodać asystenta zdarzeń on/off którego ustawimy na wejście przypisane do Pt1 i uzyskać log zmian folii.
Asystent braków
Asystenta braków który za pomocą sygnału dodaje brak do ogólnej ich puli dodano głównie dla obsługi maszyn które same potrafią usuwać braki, np. dzięki zainstalowanemu systemowi wizyjnemu sterującemu wyrzutnikiem:
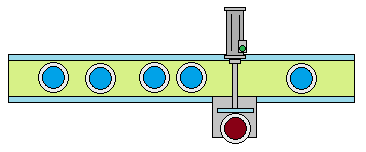
Jeśli stosujemy kategoryzację braków to asystent może zwiększać licznik braków odpowiedniej kategorii. Możliwe jest też dodawanie po impulsie na wejściu nie jednego braku a tylu baków jaka jest aktualna krotność, np. w sytuacji gdy po zidentyfikowaniu problemu po wyjęciu wyprasek z formy robot usuwa je wszystkie.
Jeśli nie mamy systemu wizyjnego może to być np. przycisk „brak” który po zidentyfikowaniu problemu naciśnie operator.
Ciekawym rozwiązaniem wydaje się też zastosowanie pojemnika ze swego rodzaju lejkiem i fotokomórką – pracownik wrzuca wadliwy produkt a fotokomórka go zlicza.
Miejsce powstawania braków
Klasyfikacja braków najczęściej określa ich rodzaj: przebarwienia, niedolania, uszkodzenia mechaniczne itp. Ale może też określać miejsce gdzie brak powstał. Mając linię produkcyjną możemy określić kategorię nalewarka, etykieciarka, pakowarka etc. Wprowadzając braki, czy to programowo, czy za pomocą asystentów mamy ogląd gdzie one najczęściej powstają.
Pomiar energii
Na rynku dostępne są mierniki zużycia energii elektrycznej wyposażone w wyjścia impulsowe na których generowane są impulsy w ilości proporcjonalnej do ilości zużytych kilowatogodzin. Golem pozwala na zliczenie tych impulsów i przeliczenie na zużycie prądu a następnie na powiązanie zużycia z daną maszyną. Zajmuje się tym asystent energii.
Konfigurację asystenta prześledzimy na przykładzie licznika LE-03 produkowanego przez firmę F&F Strona producenta: http://www.fif.com.pl
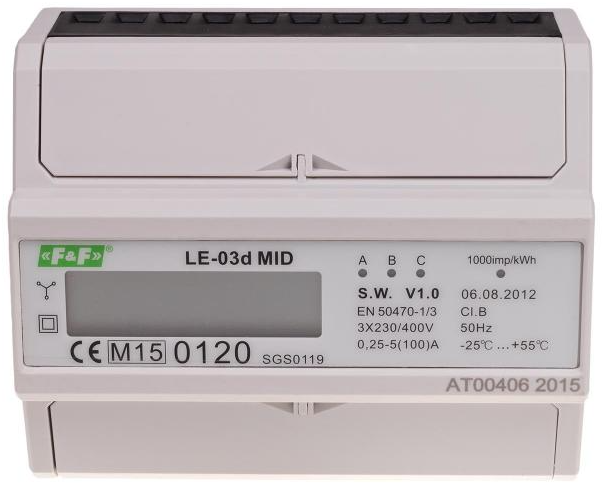
Licznik LE-03d nie wymaga stosowania zewnętrznych przekładników dla prądu do 100A a więc można podłączyć go bezpośrednio do maszyn z zainstalowaną mocą ok. 40kW. Licznik ma optoizolowane wyjście impulsowe 800 impulsów na kWh. Na zacisk plus podajemy 24V z zasilacza obiektowego a sygnał z zacisku minus podajemy na wejście koncentratora.
Problemem licznika LE-03 jest bardzo krótki impuls który przez filtry koncentratora może zostać potraktowany jako zakłócenie. Dlatego musimy skorzystać z wejść logicznych z podziałem przez 4 i dużo mniej restrykcyjnymi filtrami.
Sygnał z licznika podłączymy na wejście 6 ale w konfiguracji asystenta ustawiamy wejście 117.
Za pomocą kalkulatora liczymy przelicznik określający ilość kWh/impuls. Przy 800 impulsach na kWh i uwzględnieniu podziału wejścia logicznego będzie to 0.005 kWh na impuls.
Dostępne są liczniki, np. licznik LE-03MQ które pozwalają na programowanie ilości impulsów i ich czasu trwania. Możemy w liczniku LE-03MQ ustawić 100 imp. na kWh i czas impulsu na 200ms co pozwoli nam podłączyć licznik z pominięciem wejść logicznych których w koncentratorze mamy tylko 16.
W przypadku liczników z przekładnikami prądowymi musimy dokładnie sprawdzić jakiej przekładni dotyczy katalogowa ilość impulsów ponieważ czasami informacja ta jest niejednoznaczna.
Pobór energii jako sygnał pracy
Asystent energii może wygenerować sygnał pracy dla nadzorcy dla którego liczy energię. Mówiąc inaczej urządzenie pracuje wtedy kiedy pobiera prąd. Poza załączeniem tej funkcji nadzorca musi mieć ustawione wejście logiczne (65-111) którym sterować będzie asystent oraz ustawić czas przedłużenia impulsu tak aby uzyskać prawidłową pracę przy niskim obciążeniu.
Asystent zdarzeń on/off
Każdy nadzorca poza rejestrem powiadomień logującym wszelkiego rodzaju zdarzenia (zmiana statusu, produktu, operatora) posiada rejestr zdarzeń on/off ( załączono / wyłączono ) :
Rejestr komunikatami „zasila” asystent zdarzeń który wykrywając pojawienie się i/lub zanik sygnału dopisuje odpowiedni komunikat.
Ważne aby uniknąć „zapchania” bazy SQL w przypadku podłączenia szybko zmiennych sygnałów każdy asystent ma dodatkowe zabezpieczenie które blokuje następny komunikat na 2-3 sekundy.
Do czego może się przydać rejestr zdarzeń?
#
Jeśli maszyna ma bardzo długi cykl to możemy w asystencie ustawić to samo wejście co jej asystent aby śledzić datę i godzinę rozpoczęcia i zakończenia każdego cyklu.
#
Podłączenie osłony w maszynie CNC może nam dać obraz intensywności akcji podejmowanych przez operatora – osłonę poza załadunkiem surowca i wyjęciem materiału otwieramy po to aby dokonać inspekcji, pomiarów, oczyszczenia strefy roboczej etc.
W automacie montażowym częste otwieranie osłon może świadczyć o dyskusyjnej jakości komponentów blokujących mechanizmy i podajniki.
#
Asystent zasilania ( zobacz rozdział „energia elektryczna” ) również generuje komunikaty on/off podczas załączenia / wyłączenia zasilania urządzenia.
Nadzorca jako kontener
Sposób działania nadzorcy determinuje model a ten ma tryb maszyny lub agregatu. Ale może mieć tryb „Kontener dla asystenta on/off”. Po wybraniu tego trybu jedynym ustawieniem nadzorcy jest numer asystenta:
[img]
a tak skonfigurowany nadzorca wyświetla jedynie dwa ostatnie zdarzenia i po kliknięciu wyświetla rejestr zdarzeń.
Możemy więc prosto przygotować nadzorcę który jedynie wyświetlać będzie godziny otwarcia i zamknięcia bramy wjazdowej:
[img]
Asystent liczenia
Nadzorca wykorzystuje przypisane mu wejście zarówno do liczenia czasu pracy jak i do liczenia cykli/produktu.
Dla nadzorcy można skonfigurować asystenta który będzie liczył produkt dla niego lub za niego co oznacza że asystent może liczyć cykle jednocześnie z nadzorcą albo możemy liczenie w nadzorcy wyłączyć.
Dla jednego nadzorcy może „pracować” więcej niż jeden asystent.
Liczenie produktu z kilku torów
Wyobraźmy sobie maszynę którą produkt opuszcza w 4 niezależnych rzędach ( prowadnicach ). Aby prawidłowo policzyć produkt instalujemy 4 czujniki S1..S4 nad prowadnicami:
w nadzorcy wyłączamy liczenie załączając w modelu ustawienie „Liczenie wg konfiguracji przejmuje asystent” oraz konfigurujemy 4 moduły asystentów w trybie liczenia produktu z krotnością ustawioną na 1. Każdy przesuwający się pod czujnikiem produkt zwiększy stan licznika produktu o 1.
Wejście przypisane do nadzorcy będzie liczyło czas pracy, np. z napędu maszyny.
Rozdział liczenia czasu pracy i produktu w maszynie CNC
Maszyny pracujące cyklicznie takie choćby wtryskarki czy prasy podłączyć jest bardzo łatwo. Bez problemu znajdziemy sygnał który pojawia się cyklicznie. Gorzej jest z maszynami takimi jak obrabiarki CNC. Pracują one po kilkanaście minut i są często zatrzymywane np. w celu dokonania inspekcji czy pomiarów. Znalezienie sygnału który jednocześnie pozwalałby na liczenie efektywnego czasu pracy i ilości produktu może być trudne. W wielu przypadkach może pomóc rozdzielenie sygnałów pracy i cyklu.
Wiele maszyn CNC począwszy od tych starszych po te najnowocześniejsze mają zwykłe lampki na 24V sygnalizujące przetwarzanie programu czyli faktyczną pracę maszyny. Możemy skonfigurować nadzorcę maszyny aby liczył czas pracy w klasyczny sposób: zliczamy czas pracy gdy lampka świeci.
Czasami, szczególnie starsze maszyny, wyposażone są w elektromechaniczne liczniki produktów a czasami mają wyjścia do podłączenia takowych. Podobnie jak w poprzednim przypadku możemy wyłączyć liczenie produktu w nadzorcy i skonfigurować do liczenia asystenta który będzie obserwował wejście do którego podłączono licznik. :
Jeśli maszyna nie ma licznika albo innego sygnału który można użyć do liczenia produktu, np. z podajnika materiału czy z robota który odbiera element to możemy rozważyć użycie zwykłego przycisku który operator naciśnie wyjmując gotową sztukę z maszyny.
W wielu przypadkach, w maszynach CNC możemy wykorzystać moduły wyjść do sterowania peryferiami które można aktywować za pomocą komend w programie sterującym.
Motogodziny
Oddzielną kategorią liczników czasu są liczniki motogodzin które między innymi mogą być synchronizowane z licznikami motogodzin w programie CMMS Maszyna SMART.
Motogodziny mogą być liczone na podstawie czasu efektywnej pracy, czasu statusu PRACA, czasu gdy jest status inny niż POSTÓJ PLANOWANY. Motogodziny mogą też być liczone za pomocą asystenta motogodzin, za pomocą wejścia koncentratora.
Asystent zwiększa licznik motogodzin gdy wejście jest aktywne i może ono być połączone np. z sygnałem z pompy hydraulicznej – zakładamy wtedy że maszyna, z punktu potrzeb UR pracuje gdy pracuje pompa.
Wykrywanie obciążenia silnika
Jest wiele urządzeń które mogą pracować ale nic nie robić. Takim urządzeniem może być np. młyn do mielenia odpadów
tworzyw sztucznych. Może on pracować czyli mieć załączony silnik ale nic nie mielić. Spójrzmy na schemat podłączenia dwu młynków:
Pierwszy jest podłączony w bardzo prosty sposób – sygnał na wejście koncentratora podawany jest z przekaźnika który załączy się gdy załączony jest silnik. Jeśli silnik załączany jest stycznikiem to można zamiast przekaźnika P1 użyć styków pomocniczych. Rozwiązanie to ma wszak jedną wadę – Golem będzie liczył czas pracy zawsze gdy silnik jest załączony co jednak nie oznacza ze pracuje.
W obwód silnika 2 młynka wstawiono przekaźnik P2 który załącza się po przekroczeniu ustawionego poziomu prądu – a wiec wtedy gdy silnik wykonuje pracę. W handlu dostępnych jest wiele tego typu przekaźników np. EPP-619 produkcji F&F
W nadzorcy należy na kilka sekund ustawić filtr opóźnienia wyłączenia tak aby nie rozpoznawał on krótkich przerw sygnału który przy zmiennym obciążeniu będą się z pewnością pojawiać.
W przykładzie podłączono też sygnał załączenia silnika który może być użyty do sterowania ikoną zasilania za pomocą asystenta zasilania.
Liczenie metrów
Wiele maszyn wytwarza produkt w sposób ciągły. Przykładem może być maszyna do produkcji folii. Co prawda możemy liczyć rolki ale te „schodzą” co kilkadziesiąt minut. Dobrze było by liczyć wyprodukowane metry bieżące.
Niektóre maszyny wyposażone są w enkodery. Najprościej było by pożyczyć sobie z nich sygnał. Ale na 100% taki sygnał jest za szybki a impulsy za krótkie. Można jednak zastosować liczniki z wejściami kwadraturowymi do obsługi en koderów. Liczniki takie często mają wyjście które daje impuls co X kroków enkodera. Możemy takie wyjście ustawić tak aby wygenerować impuls po policzeniu tylu kroków enkodera która będzie odpowiadać np. jednemu metrowi materiału.
Jednak jeśli maszyna nie ma enkodera możemy zrobić go sami instalując kółko obracające się wraz z przesuwem produktu i czujnikiem indukcyjnym zamontowanymi tak że wygenerowany jest jeden impuls na obrót tego kółka:
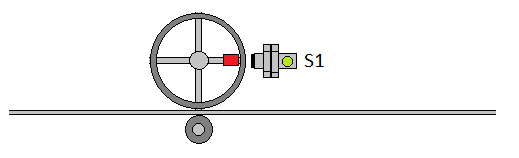
Przeanalizujemy dwa przypadki, pierwszy gdzie kółko ma obwód 1 metra, ale będzie to koło a nie kółko i drugi gdzie mamy kółko o obwodzie 28 cm.
W pierwszym przypadku mamy 1 impuls na 1 metr bieżący produktu. Parametr przelicznika ustawiamy na 1 a każdy impuls powoduje zwiększenie licznika produktu o 1 metr. W drugim przypadku gdy chcemy mieć licznik produktu skalowany w metrach musimy odpowiednio dobrać przelicznik (parametr gniazdo). Skoro 1 impuls to 28 cm to po każdym impulsie dodajemy do licznika produktu 0.28 metra bieżącego. Nie ma z tym problemu ponieważ parametr gniazdo nie musi być liczbą całkowitą więc ustawiamy go na 0.28
Pamiętajmy jednak o kilku sprawach. Po pierwsze musimy zadbać aby nie przekroczyć częstotliwości granicznej wejścia koncentratora – ze względu na filtry jest to około 4-5 impulsów na sekundę ale należy zmierzać do tego aby nie było to więcej niż 1 impuls na sekundę aby zminimalizować ryzyko „gubienia” impulsów. Można tu skorzystać z wejść logicznych z podziałem przez 4. Podłączamy sygnał np. do wejścia 1, ustawiamy dla nadzorcy wejście 112 a przelicznik powiększamy 4 krotnie do 1.12.
Następna sprawa to dokładność. Taka metoda pomiaru będzie obarczona bardzo dużym błędem na który złożą się: niedokładność pomiaru (nigdy nie będzie tak że jeden obrót to będzie 28 centymetrów - zawsze będzie to jakaś dodatkowa część milimetra która będzie dodawana do wyniku) oraz poślizgi koła pomiarowego. Dlatego im większy będzie czas dla którego wyznaczymy ilość produktu tym większa będzie odchyłka od rzeczywistości.
Biorąc jednak pod uwagę fakt że bardziej zależy nam na ocenie ilości w funkcji czasu a do policzenia wielkości produkcji jest magazyn możemy uznać takie rozwiązanie za rozwiązanie kompromisowe.
Sterowniki PLC
W systemie Golem OEE MES nie korzystamy z możliwości komunikacyjnych sterowników maszyn bo te co prawda dają coraz większe możliwości ale też potrafią sprawiać mnóstwo niespodzianek i generować duże koszty, szczególnie przy niejednorodnym parku maszynowym.
Nie oznacza to jednak że jeśli mamy odpowiednią wiedzę ( hasła tam gdzie trzeba ) to nie możemy skorzystać z dobrodziejstw sterowników PLC.
Użycie sterowników rozważać możemy w dwu scenariuszach: jako oddzielne urządzenie do kształtowania sygnałów oraz jako modyfikacje oprogramowania kontrolowanej maszyny:
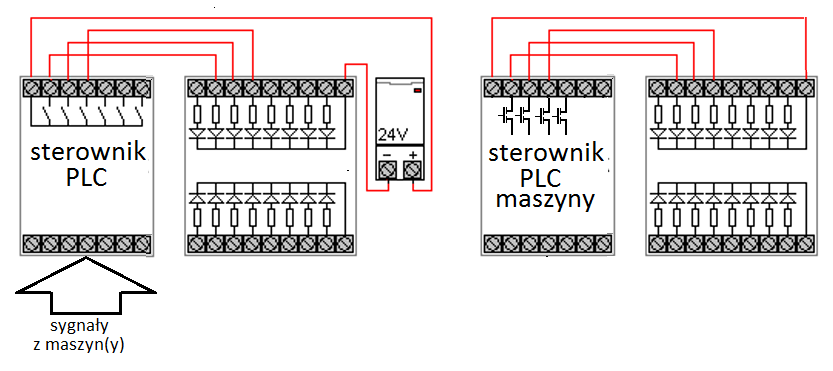
W pierwszym przypadku możemy użyć sterownik lub przekaźnik programowalny typu Logo! do kształtowania sygnałów.
W przykładzie o liczeniu metrów pisałem o pożyczeniu sygnału z enkodera za pomocą licznika. Liczniki takie można łatwo zasymulować w programie. Innym przykładem może być maszyna do gięcia profili drewnianych gdzie sterownik Logo! obserwuje kilka sygnałów i wystawia sygnał cyklu do koncentratora jeśli sygnały wejściowe pojawią się w prawidłowej kolejności i trwają określony minimalny czas.
„Zaszaleć” możemy wtedy gdy mamy możliwość zaingerowania w program sterujący maszyny i wolne wyjścia. Trzymając się przykładu enkodera możemy dodać „bloczek” dodatkowego licznika i już….
Przykładem niech tu będzie jeden z naszych klientów mających 5 linii produkcyjnych pod kontrolą dużego sterownika S7-400. Programista poza sygnałami cykli wyprowadził też po 4 wyjścia do sterowania statusem i uzupełnił pulpity operatorskie o możliwość jego sterowania z opcjami np. automatycznego dekodowania awarii.
Przeniesienie sygnałów drogą radiową
Ciekawą opcją jest przeniesienie sygnałów drogą radiową korzystając z szeregu dostępnych zestawów pilotów zdalnego sterowania. Trzeba jednak za każdym razem podejść do sprawy indywidualnie gdyż połączenia radiowe, tak wi-fi jak i klasycznych pilotów radiowych 868 lub 433 MHz mogą na hali przemysłowej spotkać przeróżne niespodzianki, np. dobrze uziemione regały wysokiego składowania.
Jeden z klientów podłączył kilka sygnałów w bardzo rozległej instalacji do produkcji łańcuchów robiąc testy w ten sposób że do każdego nadajnika podłączony był licznik. Po dwu tygodniach testów, gdy okazało się że różnice są dla użytkownika akceptowalne - „zagubiono” ok 7% impulsów”.
Z rozwiązań profesjonalnych polecamy
Radiowe łącze sygnałowe TM-05-LoRa-WI-1
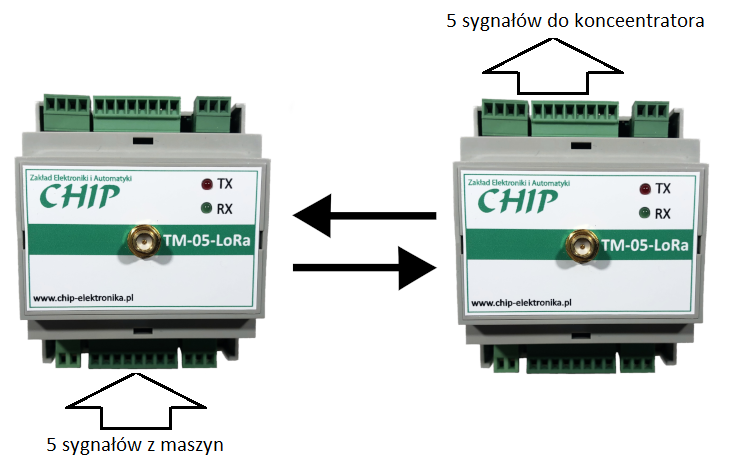
które pozwala na przeniesienie 5 sygnałów ( w obie strony plus sygnały analogowe ).
Takie rozwiązanie może być szczególnie korzystne przy podłączaniu infrastruktury, np gdy chcemy śledzić ruch na bramie wjazdowej.